ご依頼内容/要望
合板やパネル、石膏ボードなどを加工している業者様からのご依頼でした。音楽室の壁に採用されている吸音板・有孔ボードは、合板に穴をあける加工が施されています。当初、それらの穴あけはプレス加工で行われていましたが、プレス加工ですと、穴を空けた裏面にバリが発生するので、一度サンドペーパーなどで綺麗にならす必要がありました。また、穴あけのピッチを変更する際のギアアタッチメントのセット替えは、手動で行わなければならず、難しい作業ではないものの何度も行うとなるとかなりの手間になります。こうした問題により、吸音板の製作は効率があがらず生産性が悪いものでした。これらの問題を解決する加工機を制作して欲しいというのが、お客様のご要望でした。
TOYOのご提案
作業スピードのアップとバリの発生を抑えるため 列組みの多軸ドリルを採用。 サーボモーターも搭載し、数値制御で自動かつ 精度の高い加工実現をご提案。
裏面のバリの原因は、そもそもプレス加工による穴あけで発生するもの。そこで私たちはドリルによる加工を検討しました。ドリルによる精度の高い加工であれば、裏面のバリの発生を抑えることが期待できたからです。更に、深い位置まで精度の高い加工が可能なドリルは、複数枚重ねた合板も容易に穴をあけることができます。1度の加工で複数枚の加工が可能となれば、生産スピードの大幅アップも実現できます。そして、サーボモーターの搭載もご提案しました。東洋のソフト技術があれば、サーボモーターで穴あけ位置をミリ単位の位置で自由に設定することができ、お客様の事業拡大に繋がるという自信があったからです。
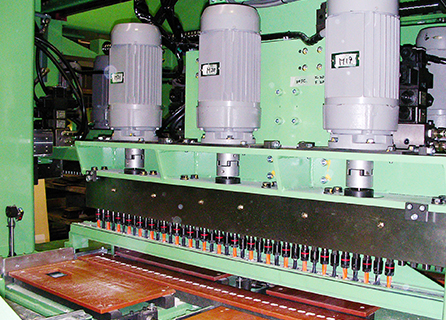
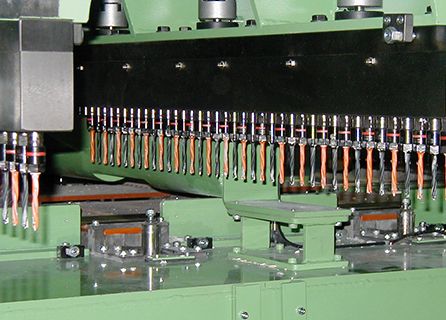
ここがポイント!
1つ目は、多軸ドリルの列組みを採用したことだと思っています。列を組んだことで、2列のドリルが同時進行で作業を行うので、単純計算2倍の作業効率を獲得することになります。
2つ目は、ギアアタッチメントのセット替えをNC指令で自動切替をするようにしたことです。手動切替の手間が無くなったことで、切替作業に割く人も時間もカットできます。こちらも作業の効率化に一役買ってくれています。
完成
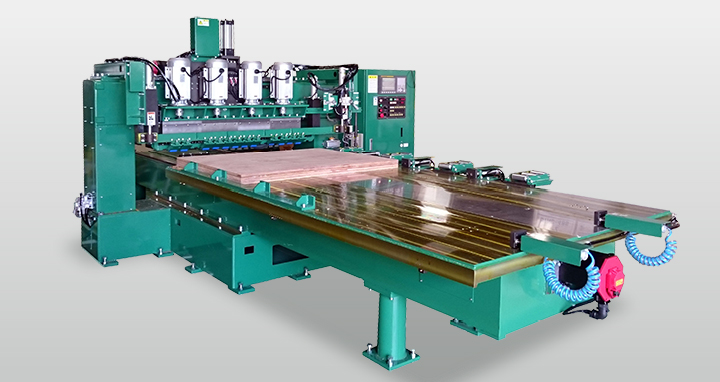
お客様の声
私たちが抱えていた問題に、求めていたもの以上の解決策をご提案していただきました。東洋鐵工所さんが開発の手綱を握りながらも、局面で話し合いを重ねながら進めていきましたので、安心して開発をお任せできました。納品・設置・施工、定期的な点検からスクランブルの修理にも対応していただき、感謝するばかりです。この専用機の導入をきっかけに会社の業績も右肩上がりとなり、2台目、3台目の開発をご依頼しています。